聚氨酯工业中使用的聚四氢呋喃多元醇多为分子量1000~3000、端基为羟基的均聚醚或共聚醚。主要的生产方法是采用氟磺酸催化体系、高氯酸-醋酸酐催化体系、发烟硫酸催化体系和杂多酸催化体系等。早期的氟磺酸催化体系,用酸量大,对设备腐蚀严重,生产成本高。目前,在该工艺的基础上,开发、使用了一种称为 Nafion的磺酸基超强树脂催化剂。原料四氢呋喃和醋酐的混合物在54℃下通过该类催化剂的固定床,停留4h,使一半的四氢呋喃转化成二醋酸二元醇酯,后者在Nafion催化剂存在下,于104℃下与甲酸进行酯交换,即得 PTMEG粗品,经蒸馏等后处理,获取 PTMEG成品。在聚合过程中,增长链段的正碳离子与酸酐或体系中生成的醋酸发生链转移反应,生成稳定的乙酰封端的聚合链,并以此控制聚醚生长的分子量,然后再用碱-乙醇溶液进行水解,使端基转化羟基。
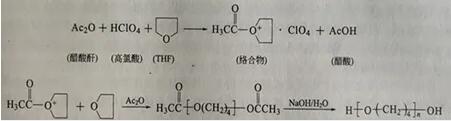
该生产方式流程长,酸酐消耗量大,对设备的腐蚀性强。
使用发烟硫酸为催化体系的生产,不需进行水解,仅一步反应就可生成 PTMEG,但对高分子量 PTMEG的合成,在引发体系中仍需加人少量高氯酸。此法的缺点仍是对设备的腐蚀性强。当然,为了降低反应体系对设备的腐蚀性,可以使用三氟化硼-乙醚络合物引发体系,但缺点是约有30%的端羟基为仲羟基,其反应活性低于伯羟基。
20世纪70年代,美、德、日等国多家公司建立了以高氯酸-醋酸酐或以浓硫酸为催化体系的聚四氢呋喃醚生产厂,以前者为例基本生产流程如图4-4。
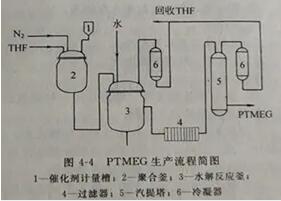
在反应釜中加人定量的四氢呋喃,在氮气保护下,由催化剂高位计量槽加入催化剂,在冰盐水夹套冷却的情况下,在0一5℃的条件进行聚合反应,然后反应液在水解反应釜中加人定量的水,于90~100℃下搅拌反应2h,使聚醚端基完全转变成羟基,未反应的单体通过冷凝器回收后进入循环使用系统。中和后的混合物分为两层,上层使用碱液中和后在过滤装置去滤除固体盐类化合物,滤液送入汽提塔,去除杂质后获得 PTMEG。
如前所述,反应也可在浓硫酸催化下进行开环聚合,但SO3浓度应控制在23%~28%(质量),若过高会使聚醚产生轻度碳化,色泽加深,而且在后处理中脱色困难。浓度过低,则聚醚多元醇收率过低。
日本旭化成工业公司使用高浓度杂多酸水溶液催化体系,进行了THF一步反应连续法生产 PTMEG,其基本反应和工艺简介如下。

将四氢呋喃和杂多酸水溶液连续送入聚合反应釜,在150~200℃反应0.5~2h,降温至60℃,反应4h,生成物经冷却、分离,催化剂可循环再利用,粗品 PTMEG液体无需水解,经过精制处理除去残余催化剂,即可获得分子量分布很窄的、色泽浅、纯度高的 PTMEG,分子量可控范围为500~3000。其产品性能完全可以满足聚氨酯纤维等高性能聚氨酯制品的需要。尽管目前此类催化剂体系还存在着催化剂用量过高,单程转化率并不理想、脱除催化剂需要消耗大量烃类溶剂等缺点,但其简单的一步反应,对设备腐蚀性小,产品分子量分布狭窄、规整性好的优点,已经充分显示出杂多酸类催化剂在 PTMEG合成中强大的竞争力。